Linear Position Sensors Reference Guide
Written by transtek_admin on 03/07/2024
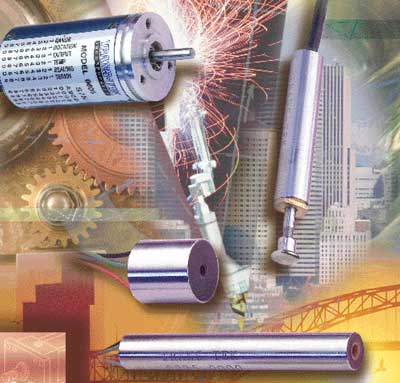
Linear position sensors play a critical role in various consumer and industrial applications, quietly supporting functionalities from robotics and automation to electronics and automotive systems. Simply put, these devices convert physical movement into electrical signals, providing valuable position data for control, monitoring, and safety purposes.
There’s a diverse range of linear position sensor technologies on the market today, each offering advantages for specific applications. Selecting the ideal one depends on several factors including the required range, resolution, as well as the operating environment and budget. Today, we’ll explore the more common position sensor types and their typical uses:
Linear Variable Differential Transformers (LVDTs):
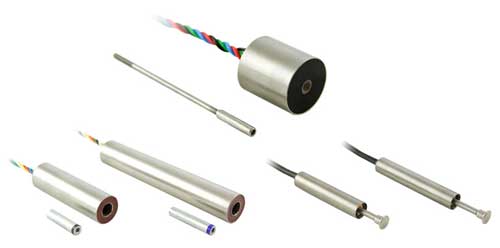
LVDTs utilizes electromagnetic induction to measure linear displacement with high accuracy and repeatability. They are relatively simple yet rugged devices, and best suited for applications with short-medium range requirements. LVDTs hold up very well in harsh environment uses including aircraft landing gear and industrial machinery due to their robust construction. They are moderately priced, and a great value overall as they stand up well to the test of time.
Spring-Loaded Linear Potentiometers (SLLP)
Spring-loaded linear potentiometers, often referred to as “string pots”, monitor and track linear motion by maintaining contact with the object being measured. They are also relatively simple components, and resistant to temperature changes and vibration. They represent a relatively cost-effective solution, however they tend to wear out quickly due to the contact element, the string, constantly being extended and retracted. You must consider lifetime cost when evaluating them for position sensing. String pots are found in applications requiring basic displacement measurement, such as joysticks, instrument knobs, and linear positioning systems with moderate accuracy requirements.
Laser-based Position Sensors
These high tech sensors use laser beams to measure distance or displacement based on light travel time, offering high speed and precision. Unlike string pots, they don’t have to touch the object being measured, and don’t wear out quickly. They provide pinpoint accuracy, and therefore can support tighter tolerances. The tradeoff? As you can imagine, laser-based solutions can be harsh on the wallet. Also, they don’t perform well in dusty or dirty environments. They are best suited for more demanding applications such as self-driving cars, 3D scanners, and high-resolution industrial measurement.
Radar Sensors
Radar sensors emit radio waves and analyze reflected signals to determine object position and movement over longer distances. Just like lasers, they don’t have to make contact, however they are harder to pinpoint. Cost range varies based on the type, but note that they can get expensive. They are ideal for applications requiring long-range detection and tracking including air traffic control, speed guns, and weather monitoring systems.
Additional Linear Position Sensing Technologies
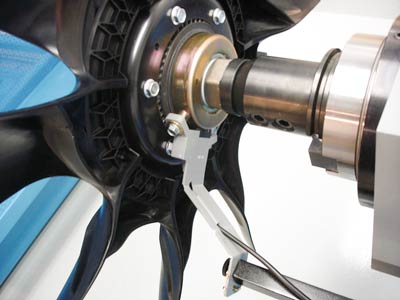
In addition to these more popular approaches, numerous other position sensor technologies exist, each designed for specific needs. These include:
- Magnetostrictive Sensors – utilize magnetic fields to measure linear displacement with high resolution. They are employed for many uses including liquid level measurement, paper converting, and metalworking.
- LiDAR – similar to RADAR technologies, LiDAR emits pulsed light waves, which bounce off surrounding objects, and return to the sensor. It’s a relatively expensive approach to position sensing, but does offer high accuracy. LiDAR is used in robotics, automotive, and aerospace applications.
- Capacitive and Inductive Position Sensors – capacitive position sensors measure changes in capacitance to determine position, while inductive sensors rely on changes in a magnetic field that is induced in the sensor’s coils. Both sensors are usually used for very short range, high precision applications. Capacitive sensors are often found in the semiconductor industry, while inductive are found in automotive, aviation, and human interface applications.
- Hall Effect Sensors – similar to inductive sensors, Hall Effect units rely on magnetics to determine position. While they offer higher accuracy levels, hall effect sensors do not perform well in high temp environments. They are often used for research, industrial applications, and in the automotive industry.
Selecting the Right Linear Position Sensor
To choose the best sensor for your particular applications, start by answering the following questions:
- Accuracy and resolution requirements: How precise and detailed must the position measurement be?
- Measurement range: What is the expected displacement or travel distance of the object?
- Environmental conditions: Will the sensor operate in harsh environments with extreme temperatures, dust, vibration, pressure, or salinity?
- Cost and power consumption: What’s the budget? How much power can the system supply?
By understanding the many types of linear position sensors and their technical characteristics and limitations, you can make an informed selection of the optimal approach for your application – from the simplest to the most demanding.
Hall Effect Image by Figushki, under creative commons license.