Linear Velocity Transducers and Their Typical Uses
Written by transtek_admin on 07/28/2023
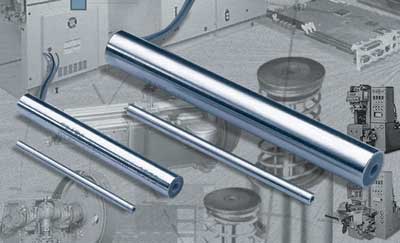
A linear velocity transducer (LVT), simply referred to as a transducer, is used to measure dynamic velocity. It achieves this by converting velocity into a voltage output. It is a rather simple device that consists of a magnet that moves through a wire coil. In this case, velocity and voltage are in a synchronous relationship: as one increases, so does the other. The faster the magnet moves, the higher the resulting voltage. They do not require input power in order to function.
As with many simple solutions, these devices can last a long time, often enduring decades of work. However, the magnet can eventually start to lose its charge, depending on the specific use. The only major limitation for velocity transducers is that their range is limited to the size of the unit itself. For instance, the maximum manufactured length for ours is about two feet long. Greater lengths can be accommodated by different technology, which we will discuss in a minute.
Velocity Transducer Applications
Despite this limitation, velocity transducers are used in wide range of applications and industries as follows:
Pipette Drawing / Custom Test Tubes – this process requires specialty machinery that allows users to fabricate custom test tubes. The machine must draw the glass in a precise, consistent manner to properly shape the test tube. In order to do such delicate work, maintaining a specific drawing speed is mandatory. This is where the velocity transducer comes in, which is used to measure the drawing speed.
- Large Guns, Missile Testing, Rocket Launchers – Guns and missile/rocket launchers contain a spring loaded start that launches the projectile. For these applications, the transducer is hooked to the spring to make sure it functions correctly and consistently. It does this by measuring how much velocity it is launching and if it’s high enough for proper projection. It’s interesting to note that with missile testing, other devices have been tried, but got destroyed in the process. The transducer satisfies the need to collect accurate speed data, and stay intact.
Shock Absorber Testing Machines – Automotive makers and race car teams must test their shock absorbers. This is done using testing machines which contain transducers that record how quickly they compress and release the shocks. While the shock absorbers take a beating in the process, the transducers hold up well over time.
- Drilling Applications – modern drilling machines, controlled by PC boards, need to maintain specific speeds for their intended applications. They contain a transducer that measures the rate that the drill is cutting through the material. The requirements for this particular application tend to get pretty intense. While standard velocity transducers are extremely durable, they can be ruggedized further for more demanding drilling situations.
Alternative Velocity Measurement Approaches
There are a multitude of ways you can collect speed data, depending on the object you want to measure. For instance, when measuring the speed of a bullet, you need to use a non-contact approach. Specifically, one that has conductive sensors, that take a measurement at point A and point B, then calculates the time in between to arrive at velocity. Although these solutions are expensive, the user may be left with few, if any, reliable alternatives. Let’s take a deeper look into some other approaches:
- Lasers – are a very accurate way to measure speed. You’re certainly familiar with the most popular use – police officers capturing vehicle speed. Laser systems are precise, but can also get costly. However, for measuring longer distances beyond the capabilities of a velocity sensor, they are often a sensible choice.
- Ultrasonic Methods – these systems work by emitting sound waves that are reflected back to the device, which calculates distance based on the time it takes. They boast a shorter range than lasers, and are not as fast. They are typically used in manufacturing operations.
- Beam Breakers – with this approach, the object being measured blocks the light and trips the sensor. Two lights must be tripped to get a measurement.
- Accelerometer Sensors – are the most recently adopted technology. They measure the acceleration forces on an object. As such, they are more suitable for monitoring vibration instead of speed. They are not as rugged as transducers, and are typically used for measuring seismic activity, inclination, and machine vibration.