LVDT Design Considerations for Pressure Vessel Applications
Written by transtek_admin on 05/17/2024
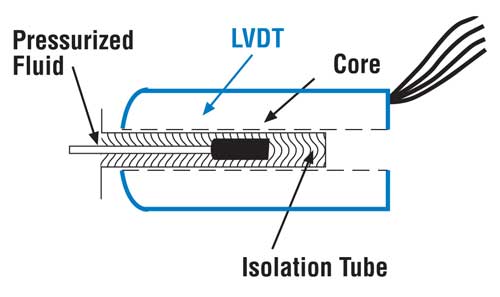
Many applications call for LVDTs to be mounted in a pressure vessel. Certain design considerations must be made so the LVDT can still perform well under higher pressures, or when there are subject to significant changes in PSI. While the highest amount of possible pressure is of key concern, other environmental and operating factors, such as temperature and magnetism, must be evaluated and planned for when specifying an LVDT.
In a perfect world, all LVDT applications, including high-pressure ones, could be satisfied by a standard or slightly modified version. Due to the range of applications and environmental conditions, this is simply not the case. While some uses could rely on a slightly modified LVDT, many call for semi-custom, and in some more extreme cases, completely custom LVDT system designs.
What Is A Pressure Vessel?
Pressure vessels come in many shapes in sizes, from small tanks to larger industrial vessels. They typically contain liquids, gases, or vapors at a pressure much higher than the surrounding pressure. A great example of an LVDT in a pressure vessel those found in hydraulic actuators used in industrial equipment. They are found on molding machines, drilling machines, and countless other large pieces of manufacturing equipment. Typically, they are very sizeable and are moving something extremely heavy. Pressures on these assemblies range from 500PSI, but can be in excess of 35,000PSI!
LVDT Pressure Vessel Mounting Approaches
There are essentially two ways to integrate an LVDT into a high-pressure vessel setup. The more obvious approach is to ruggedize the unit, making it directly capable of handling the pressure. Alternatively, a separate isolation vessel can be used. Let’s take a closer look at both methods:
Ruggedized LVDT Solutions
Modifications can be made to standard LVDT designs to help them handle high-pressure applications. The most effective way to achieve this is by making the housing stronger, using thicker and heavier materials. While this results in a bulkier unit, it can withstand higher pressures. Other design modifications could be made, including how the unit is sealed.
LVDT Isolation Vessels
In cases where there is simply not enough room for the LVDT to be placed inside the protected vessel, or the pressure is too high, an isolation vessel may be used. (Shown above.) With this approach, the main vessel will contain a port that the LVDT slides into. This way, the LVDT is not exposed directly to the pressure, but its extension rod is still able to make contact. Some of the applications require LVDT’s that are completely customized – rather than modifying a stock design.
Integrate LVDT’s Early in the Process!
As you can see, there are many considerations that must be made when designing an LVDT into a high pressure vessel. One extra word of caution – please make sure that the LVDT configuration and placement isn’t an afterthought. Be certain to integrate LVDTs into your designs early, to avoid unnecessary revisions later. Be mindful of maximum pressure, temperature, and magnetism. Source accordingly. Doing so will help ensure the precision, accuracy, and durability that LVDTs are well known for.